Comprehensive Guide: What is Porosity in Welding and How to avoid It
Comprehensive Guide: What is Porosity in Welding and How to avoid It
Blog Article
Porosity in Welding: Identifying Common Issues and Implementing Finest Practices for Prevention
Porosity in welding is a pervasive issue that frequently goes unnoticed till it creates substantial issues with the stability of welds. This common defect can endanger the stamina and toughness of welded frameworks, positioning safety risks and bring about costly rework. By recognizing the source of porosity and executing efficient avoidance methods, welders can significantly boost the quality and integrity of their welds. In this discussion, we will explore the key aspects adding to porosity development, analyze its harmful impacts on weld efficiency, and discuss the best practices that can be adopted to reduce porosity occurrence in welding procedures.
Usual Reasons For Porosity

Making use of unclean or damp filler products can present contaminations right into the weld, adding to porosity concerns. To mitigate these usual causes of porosity, comprehensive cleaning of base steels, appropriate securing gas selection, and adherence to optimal welding criteria are necessary methods in achieving high-grade, porosity-free welds.
Influence of Porosity on Weld High Quality

The existence of porosity in welding can dramatically jeopardize the architectural honesty and mechanical residential properties of bonded joints. Porosity creates spaces within the weld steel, weakening its general toughness and load-bearing capacity.
One of the main effects of porosity is a decrease in the weld's ductility and toughness. Welds with high porosity levels have a tendency to show reduced impact stamina and minimized capacity to flaw plastically before fracturing. This can be particularly concerning in applications where the bonded parts are subjected to vibrant or cyclic loading problems. Porosity can hamper the weld's capacity to properly send pressures, leading to early weld failure and prospective security risks in important frameworks. What is Porosity.
Finest Practices for Porosity Prevention
To improve the architectural honesty and quality of welded joints, what details measures can be executed to decrease the occurrence of porosity during the welding procedure? Making use of the correct welding method for the details product being welded, such as readjusting the welding angle and gun position, can additionally avoid porosity. Normal evaluation of welds and prompt remediation of any type of problems recognized during the welding process are vital methods to protect against porosity and generate top quality welds.
Value of Appropriate Welding Strategies
Carrying out proper welding strategies is vital in guaranteeing the structural honesty and top quality of welded joints, try here building upon the structure of effective porosity avoidance procedures. Excessive warmth can lead to raised porosity due to the entrapment of gases in the weld swimming pool. In addition, making use of the appropriate welding parameters, such as voltage, existing, and travel rate, is important for attaining audio welds with very little porosity.
Moreover, the option of welding process, whether it be MIG, TIG, or stick welding, should straighten with the details needs of the job to guarantee optimum results. Appropriate cleansing and preparation of the base steel, as well as picking the right filler material, are additionally important parts of proficient welding strategies. By sticking to these best techniques, welders can reduce the try this out danger of official site porosity development and produce top notch, structurally audio welds.
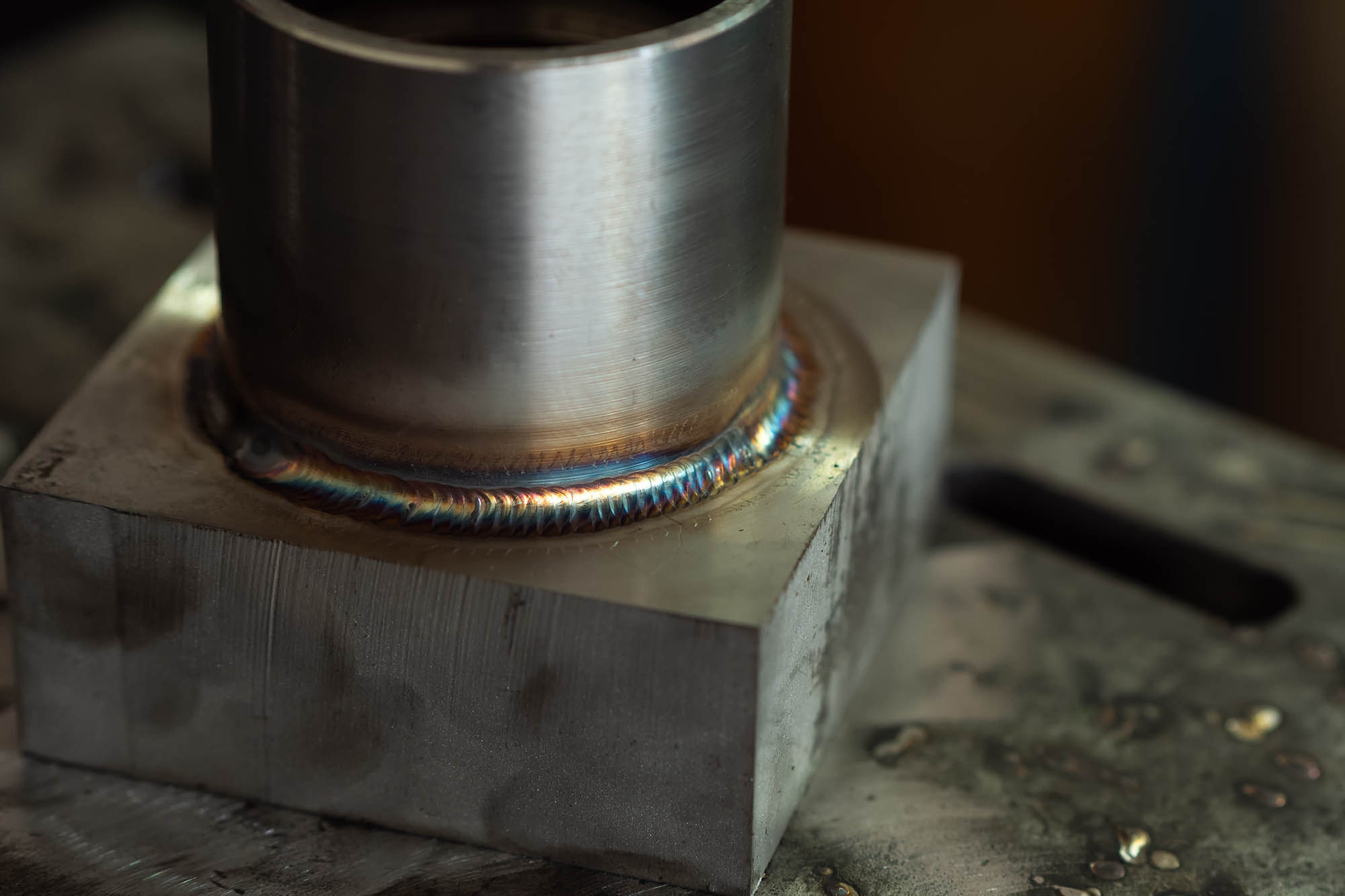
Testing and Top Quality Control Actions
Evaluating procedures are necessary to identify and protect against porosity in welding, ensuring the strength and resilience of the final product. Non-destructive testing methods such as ultrasonic screening, radiographic screening, and aesthetic examination are generally used to recognize possible flaws like porosity.
Carrying out pre-weld and post-weld evaluations is also critical in keeping high quality control standards. Pre-weld inspections entail confirming the materials, tools setups, and cleanliness of the workplace to avoid contamination. Post-weld inspections, on the various other hand, evaluate the last weld for any type of problems, including porosity, and verify that it meets defined requirements. Implementing a detailed quality assurance strategy that includes detailed testing procedures and assessments is paramount to lowering porosity issues and making certain the general top quality of welded joints.
Verdict
In final thought, porosity in welding can be an usual concern that impacts the high quality of welds. By recognizing the common root causes of porosity and carrying out best practices for prevention, such as correct welding techniques and testing procedures, welders can make certain high quality and trustworthy welds. It is important to prioritize prevention techniques to decrease the event of porosity and maintain the stability of bonded frameworks.
Report this page